Holding Torque Stepper Motor 2N.M Nema 23 Hybrid Stepper Motor 57mm
1.8 Degree
Description of NEMA23 hybrid stepper motor
- Forward/Reverse Rotation,Pause and Hold
- The forward /reverse rotation of the stepping motor can be
controlled by the input sequence of the controlled electric pulses.
- In the case of the a stepping motor lock(the motor winding is
energized,there is no external electric pulse command),the stepping
motor can still maintain a certain torque output.
- Longer Life
- Stepping motor is a mechanical structure,which does not need be
changed by electric brush or Hall sensor,thus reducing the
probability and increasing the motor life.Stepping motor life
usually determined by the life of the bearing.
- Electromagnetic furnace optimization design, lift torque, reduce
temperature rise, so that the motor running smoothly
- Accurate position Control
- The angular displacement of the stepping motor can be precise
controlled by the number of electrical pulses.Angle accuracy can be
controlled within ±0.09°without any feedback devices.
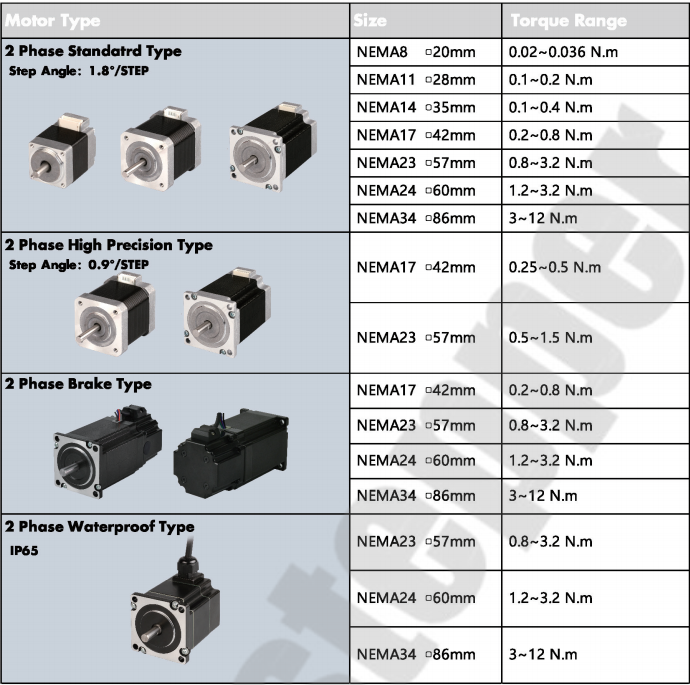
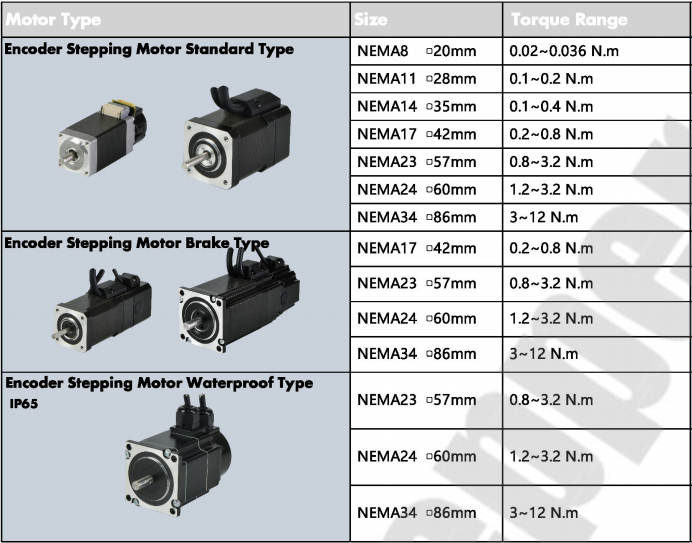
Hybrid stepper motor's specifications
- Stepping Accuracy: ± 5%
- Resistance Accuracy: ± 10%
- Inductance Accuracy: ± 20%
- Temperature Rise: 80°C Max.
- Ambient Temperature: -20°C ... +50°C
- Insulation Resistance: 100MOhm min. 500V DC
- Withstand: 500V AC, 1 Minute
Mode No | PST60H248-4P20 | PST60H248-4P30 | PST60H248-4L40 |
Holding Torque | 1.1N.m | 1.1N.m | 1.1 N.m |
Related Current | 2A/Phase | 3A/Phase | 4A/Phase |
Resistance | 1.7Ω/Phase | 0.6Ω /Phase | 0.38Ω/Phase |
Inductance | 3.9MH/Phase | 1.5MH/Phase | 0.78MH/Phase |
Inertia | 240g.cm2 | 240g.cm2 | 240 g.cm2 |
Weight | 0.6kgs | 0.6kgs | 0.6kgs |
Length | 47mm | 55.5mm | 76.5mm |
Connection | P | P | L |

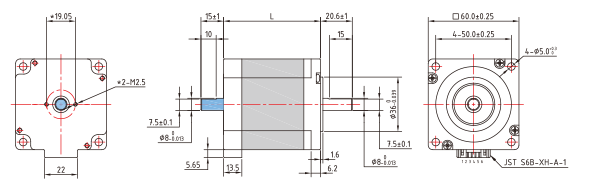
Applications of 1.8 degree Stepper Motor
- Our products are widely used in 3d and inject printers, CNC
routers, Engraving Machines, Stage Lighting Control, Security
Surveillance, Video Equipment, Laser workstation, Carving Machine,
Office Automation,Smart Toy, Digital Controlled
Machinery,Analytical and Medical Instruments, Textile Equipment,
Embroidery Machine, Precision Telescope Positioning Systems, High
Speed Dome Camera,Robotic and other automatic equipment.
Working principle of stepper motor
- To make the motor shaft turn, first one electromagnet is given
power, which makes the gear’s teeth magnetically attracted to the
electromagnet’s teeth. The point when the gear’s teeth are thus
aligned to the first electromagnet, they are slightly offset from
the next electromagnet. So when the next electromagnet is turned ON
and the first is turned OFF, the gear rotates slightly to align
with the next one and from there the process is repeated. Each of
those slight rotations is called a step, with an integer number of
steps making a full rotation. In that way, the motor can be turned
by a precise. Stepper motor doesn’t rotate continuously, they
rotate in steps. There are 4 coils with a 90o angle between each
other fixed on the stator. The stepper motor connections are
determined by the way the coils are interconnected. In a stepper
motor, the coils are not connected. The motor has a 90o rotation
step with the coils being energized in a cyclic order, determining
the shaft rotation direction. The working of this motor is shown by
operating the switch. The coils are activated in series in 1-sec
intervals. The shaft rotates 90o each time the next coil is
activated. Its low-speed torque will vary directly with current.
How to overcome the vibration and noises of 2-phase hybrid stepper
motor when rotating at low velocity?
The vibration and noise of the stepper motor rotating at low
velocity its the intrinsic defects, which can be generally overcome
by adopting following schemes:
- If the stepper motor works at resonance region, the resonance
region can be evaded by changing mechanical transmissions such as
velocity ratio.
- Use subdivided driver, which is the most common and simple method.
- Replace for the stepper motor with smaller stepping angle, like
3-phase or 5-phase stepper motor.
- Replace for AC servo motor, which can nearly overcome vibration and
noise, but the cost is quite high.
- .Add magnetic damper to the shaft of motor, such product has been
available in the market, but the mechanical structure is changed a
lot.
Buter's concern
1. All stepper motors have CE and RoHS certification
2. All motors are tested by a toasting machine for 72 hours
3. All the motors will be shipped after testing
Can you make the motor with customized requirement ?
YES. We have experienced R&D capability and great engineers,
Their experience and innovation capability can support customized
project.
2. Can you provide the samples?
YES. We can provide the samples, The delivery time is about 7-15
days according to which kind of motor you want
3. What is your MOQ?
It's accordingly to the motor type you order, Our MOQ for gear
motor can even 1pc.