APG machine
1.Clamping plate size: 1250*800mm
2.main clamping force: 400KN
3.Max opening stroke: 1200mm
4.top cylinder force: 30KN
5.bottom force: 30KN
6.Heating power: 24KW
8.With touch screen to control side
injection
7.Gross weight: 8000KG
8.Machine tilting: 5° by hydraulic X axisProduct Description
Product Description
Injection trolley and mixing with APG machine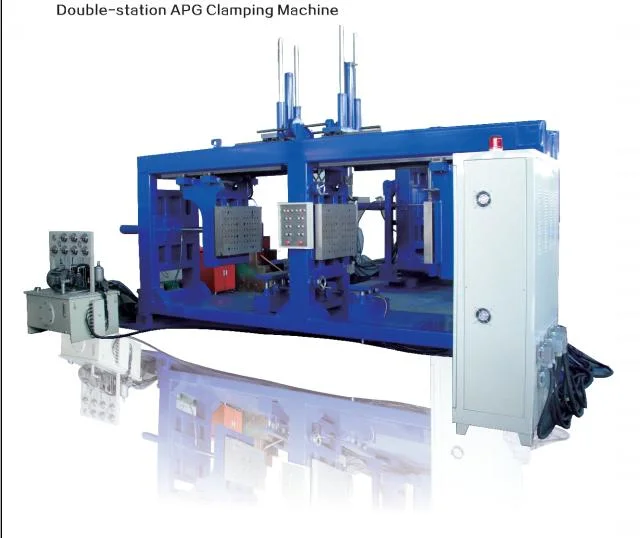