Prefabricated Pipe Gas Plant Pipe Spool Fabrication System Pipe
Prefabricated Pipe Dn500 A234 Wp91 Customized Pressure Vessel Power
Plant Pipeline
WHAT IS PIPE PREFABRICATION?
Pipe prefabrication is manufacturing pieces of pipelines in a
factory instead at the construction site. This enables utilization
of better tools and working conditions. This results in higher
productivity and better quality. It also reduces the lead time at
the construction site.
Factory prefabrication procedure
1: Main steam pipeline (two high-temperature and high-pressure
steam pipelines between the outlet header of the superheater and
the high-pressure main valve interface);
2: Hot reheat steam pipes (two high temperature and high pressure
steam pipes from the outlet header of the reheater to the interface
of the medium pressure main valve);
3: Cold and reheat steam pipes (two high-temperature and
high-pressure steam pipes between the steam exhaust port of the
high-pressure cylinder and the inlet header interface of the
reheater);
4: High-pressure water supply pipeline (the high-pressure boiler
supply water pipeline between the outlet of the electric feed pump
and the header interface of the inlet of the economizer)
The four major pipelines refer to the main steam pipeline, the
reheat hot section steam pipeline, the reheat cold section steam
pipeline and the main water supply pipeline in the high temperature
and high pressure steam water pipeline.
Factory prefabrication refers to the detailed decomposition of the
power station pipeline design drawings provided by the design
institute in accordance with the relevant standards and regulations
for thermal power plant construction, and the use of equipment,
technology, and processes (bending, beveling, welding, heat
treatment, Marking, cleaning, painting, protection, inspection) and
other advantages for piping. The model of pipeline factory
prefabrication has been widely used in power plant construction and
has shown many benefits.
The key work of pipeline factory prefabrication is elbows: a large
number of standard elbows are used in the layout design of power
pipelines, and welds are required at both ends of the elbows.
Especially the in-service inspection after the operation of the
power station consumes a lot of manpower and material resources.
Moreover, the standard elbow has almost no straight section, and
the welding seam is located at the arc starting point during
welding, which is the place where the fluid scours and the
alternating stress is the highest. Therefore, the use of elbows
instead of elbows has become the consensus of more and more people
in the industry.
The four major power pipes are high-pressure thick-walled pipes,
and the traditional bending processes are mostly hot bending and
pressing. Hot bending is to use medium and high frequency power to
locally inductively heat the circumference of the pipe material to
above the phase transition temperature, and then bend the pipe
material along the preset track to a certain curvature radius and
angle under the action of external force. The disadvantage of this
process is that the heating speed is slow, the temperature of the
inner and outer walls is uneven, the temperature difference is not
well controlled, and an oxide layer is formed on the surface of the
tube. High consumption, pollution and low efficiency. Press bending
is the pressure of the hydraulic press to press down the pipe
material through the upper mold, so that the pipe material is
plastically deformed to obtain a curved pipe similar to the shape
of the lower mold. The arc made by this simply supported beam
principle is not a standard arc, so it is difficult to control and
measure the bending radius accurately. During the pressing process,
the inner arc side of the tube material is compressed and the outer
arc side is pulled, and without compensation measures, it is
difficult to control the thinning amount of the pulled surface.
Also difficult to control.
With the development of the electric power industry, the
specifications of the main steam pipes of the supercritical and
ultra-supercritical units have reached ID425X 129, and the
specifications of the main pipes of the reheating hot section have
reached ID883X72. Materials: ASTM, A335, P92. The defects of the
traditional hot bending process are becoming more and more obvious:
the thickness of the pipe wall is increased, especially when it
reaches more than 10mm, the temperature difference between the
inner and outer walls of the pipe during the bending process is too
large, and it is difficult to meet the production requirements; the
requirements for hydraulic equipment are even higher. It is also
difficult to ensure the quality of the elbow, which brings huge
challenges to the electric power escort industry.


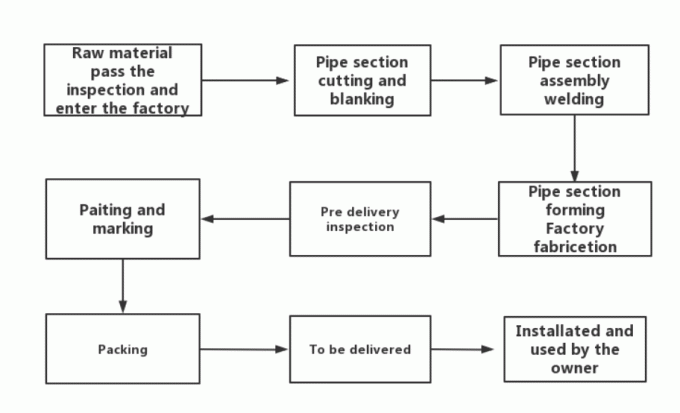
In industrial construction projects, the workload of pipeline
construction is large, the requirements for building quality are
higher and higher, and the number of pipeline construction tasks is
doubled. However, the pipeline construction procedure is complex
and the number of components is huge. When the pipeline
construction conditions are met, the construction period for
pipeline installation is short and the task is heavy, and the
phenomenon of rush for construction period often occurs. The
industrialized prefabrication of pipeline is very important.
Pipeline factory prefabrication is deeply valued by the same
industry because of its advantages of short construction cycle,
high production efficiency and high welding qualification rate,
which greatly improves the construction efficiency and construction
quality.
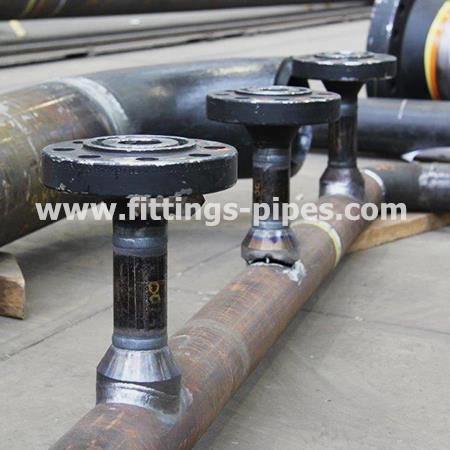



